Startup
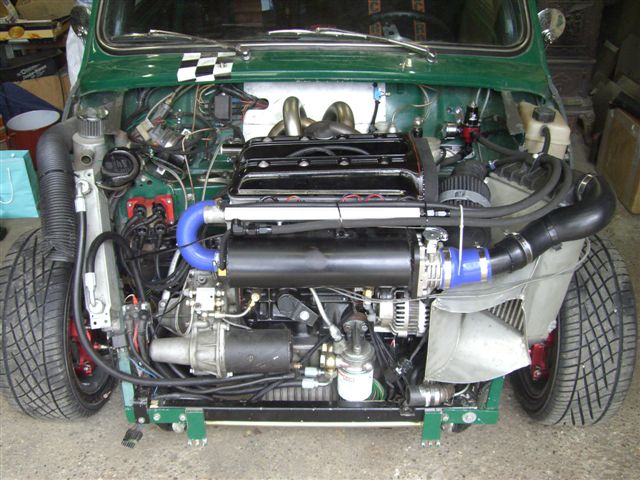
<click on the picture>
|
Some
vid`s of the startup |
Assembly
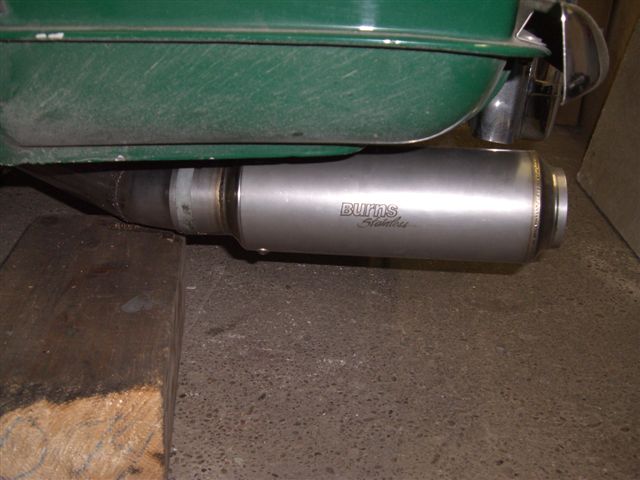
<click on the picture to get more
pics>
|
Crank sensor, electric water pump, fuel
pressure regulator,
exhaust, mounting the engine
management, injectors,
plenum, ignition
|
Exhaust
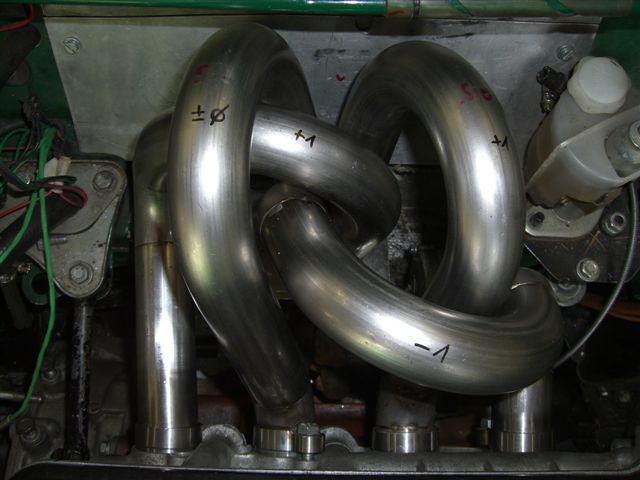
<click on the picture to get more
pics>
|
The
“Gordian knot” is ready to feed the hungry turbine. It is made of mandrel
bend stainless
steel bends, the primaries are equal length 20” +/- 0.4”. I was
trying to use as few parts as possible to reduce the number of
welds – would
not do it this way again – wasn’t worth the
hassle.
Each primary received a thermocouple bung, also a bung for
measuring
turbine inlet pressure was added to judge different
A/R housings. |
Inlet system
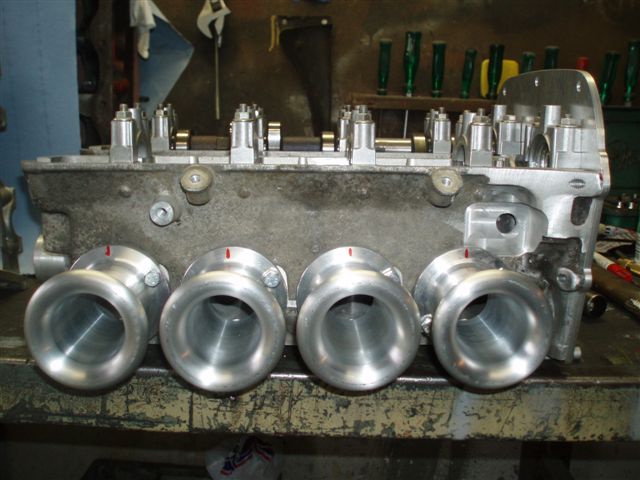
<click on the picture to get more
pics>
|
The
plenum is finished. The throttle body was “borrowed” from a
Jeep;
it is very compact and also has a build in stepper motor
for good idle control.
|
In car test
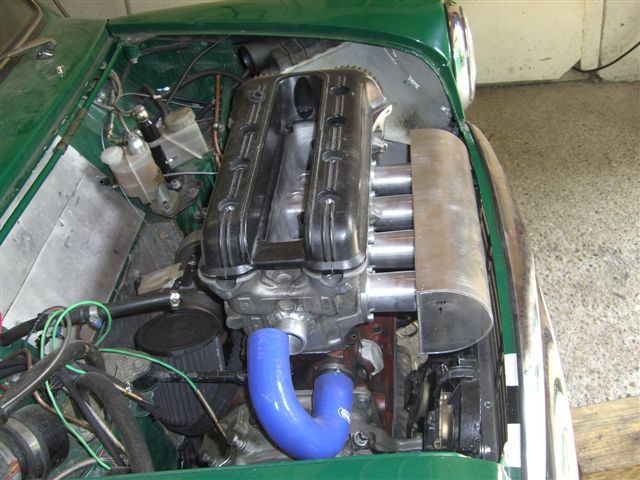
<click on the picture to get more
pics>
|
I
did not believe my eyes that I still could use the original
bonnet with my
adapted Honda pulleys, but there is only about
5mm space left between the
bonnet and the edge of the BMW valve
cover.
|
16V Bimmer head
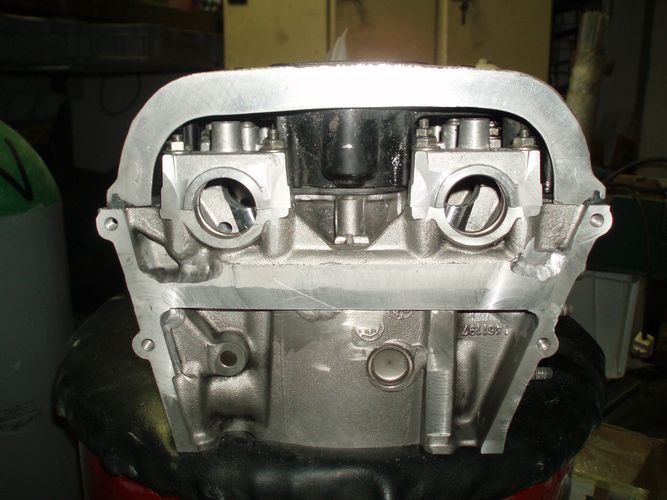
<click on the picture to get more
pics>
|
The coolant flow was changed to a more efficient path; also the floor
of the inlet ports was welded and
raised to improve airflow. The water
outlet of the head will be
positioned new to avoid air pockets;
an ECU
controlled electric water pump will control water temperature.
Some
welding and milling had to be
done to accept the new side cover. |
Clutch plate
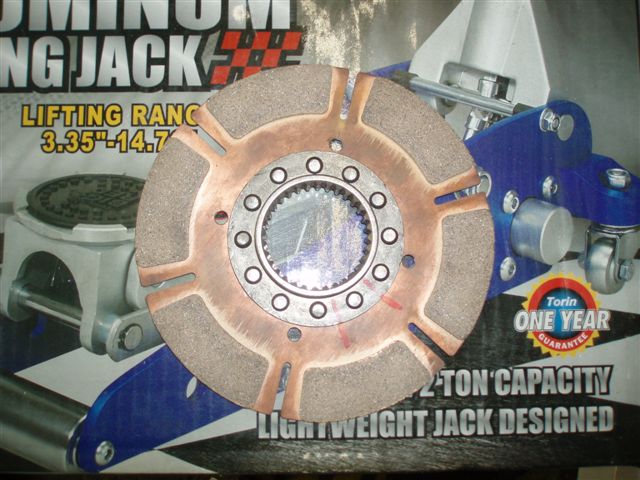
<click on the picture to get more
pics>
|
A
Tilton sinter metallic clutch plate was modified to accept the
Mini centre.
Luckily a friend of mine is working at MIBA, where these plates
are
produced for Tilton.
|
Crank
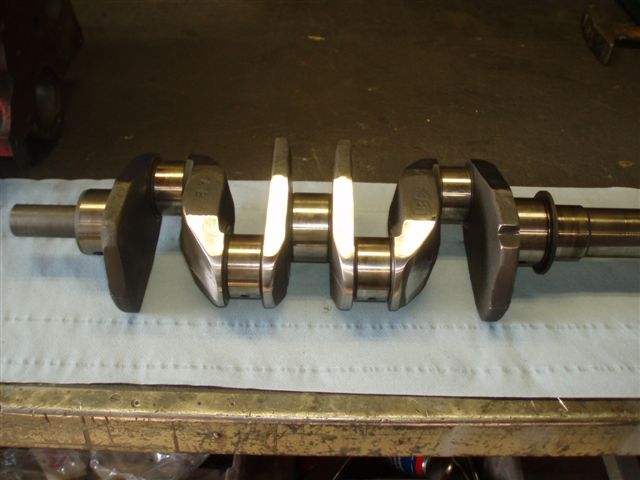
<click on the picture to get more
pics> |
The
crank was wedged to receive a better weight distribution of the
counterweights.
|
Turbo
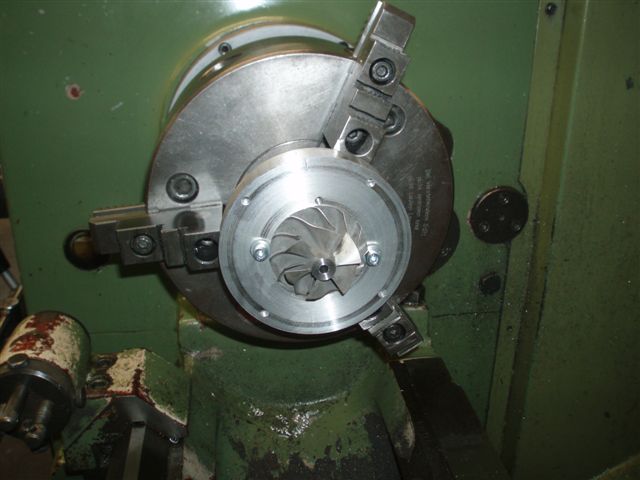
<click on the picture to get more
pics> |
I
built a hybrid turbo with a bigger and better compressor (with
very good
and broad efficiency islands), therefore I had to
reduce the height of the
wheel a little bit. The
setup was balanced after assembly.
|
Oil pump drive (cam?)
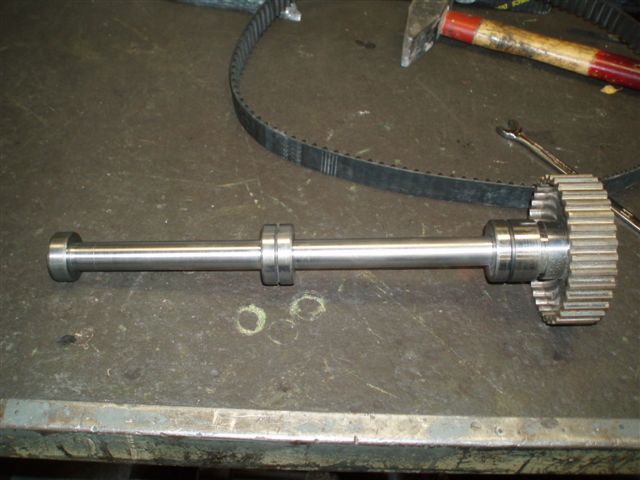
<click on the picture to get more
pics> |
The
hottest cam an A-Series has ever seen: 360°! I turned the lobes
down
in the late at my machinist – the faces of the other
customers that day were
priceless.
|
Con rods
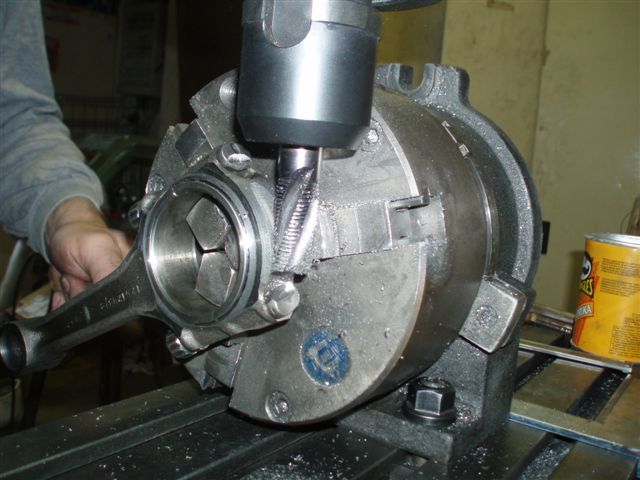
<click on the picture to get more
pics> |
Innocenti rods have been lightened to about 590g; here some
pictures before
polishing.
Forged Omega 15cc pistons will be fit
to these rods.
|
Block modifications
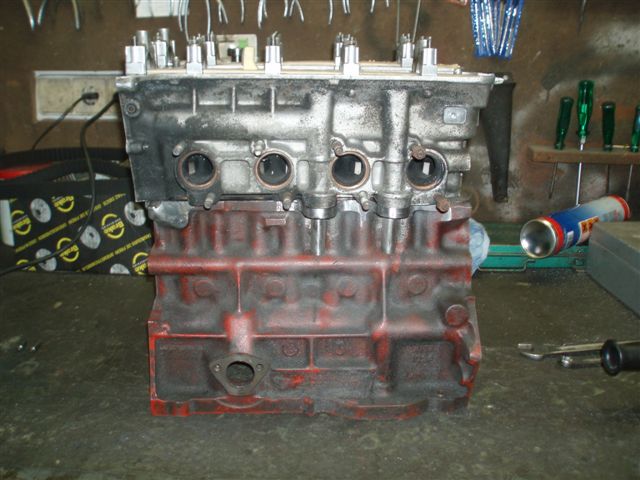
<click on the picture to get more
pics>
|
a)
The original holes were threaded and closed; then the new
threads made
for the ARP bolts.
b)
Piston under crown spray jets will find their way into this
block again.
c)
For the oil return I welded some “ears” to the block, then 2
tubes where
pressed in, to obtain a trouble free system. So I
still can use the original
BMW steel head gasket. Oil supply for
the head was also relocated slightly.
My
machinist loved me for doing that (when he had to deck the
block),
because the material hardened up in the welding area of course.
d)
The block was bored and honed with a torque plate to obtain
round bores
when the head is torqued down. But bore measurements
after removing this
plate showed that it wasn’t worth the
effort. |
Covers
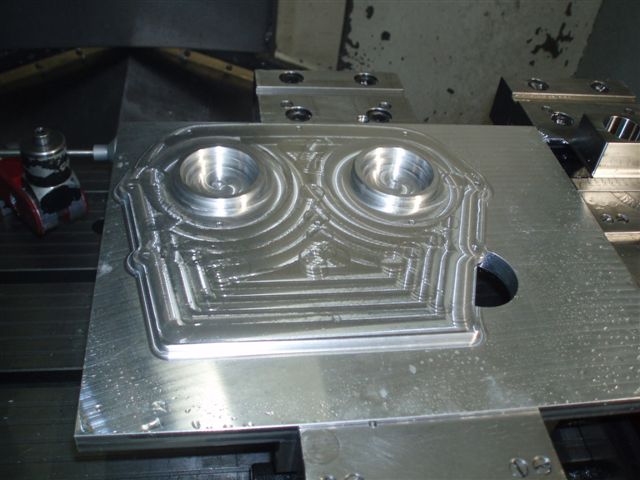
<click on the picture to get more
pics> |
Constructed by myself, milled by my brother on a CNC. For these
nice parts
I had
to learn
to work with CAD. Took me a lot of
time to learn CAD and
construct
these parts. I
was
trying to get my pulleys as near as possible to the
first
cam bearing to reduce the leverage
and therefore load for this
bearing.
|
Cam pulleys (3x)
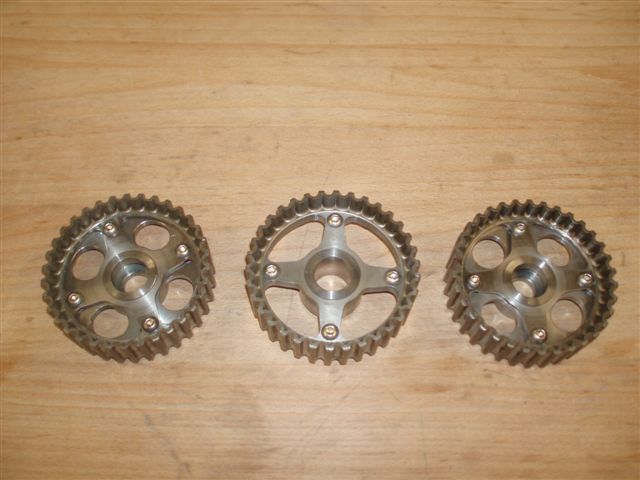
<click on the picture to get more
pics> |
Modified Honda wheels; I took them because they have a small
diameter and
I got
them
for free from a friend who is modifying
Honda engines. Cam timing
is adjustable
of course.
Bottom Honda pulley was modified and pressed on a
custom part.
|
Backplate
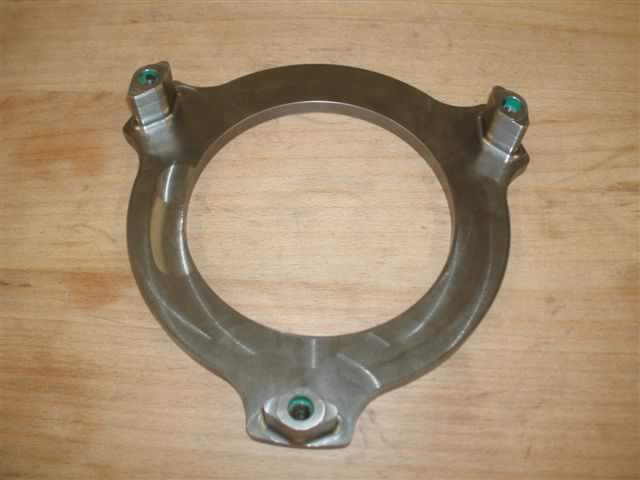
<click on the picture to get more
pics> |
Lightening was also done in a CNC mill; I also did a lot another
22G270
backplates
for
my Mini friends at this time, so we could
reduce the costs
for milling.
|
Engine management
<LINK> |
A
Megasquirt EFI will find its way into my car for fuel and spark
control.
<schematic
diagram>
|